Physical removal of contaminants
This is a guide to the treatment processes based on the physical removal of contaminants through filtration, settling (often aided by some form of chemical addition) or biological removal of microorganisms. Usually, treatment consists of a number of stages, with initial pre-treatment by settling or pre-filtration through coarse media, filtration followed by disinfection. This is called the multiple barrier principle.
Filtration
Turbidity and algae are removed from raw waters by screens, gravel filters, slow sand, rapid gravity filters or cartridge filters. Many small private supplies will rely on cartridge filters consisting of a woven or spun filter within a housing.
Pressure filters
Pressure filters are used where it is necessary to maintain hydraulic head in order to eliminate the need for additional pumping. The filter bed is enclosed in a cylindrical shell. Small pressure filters capable of treating up to approximately 15m³/h can be manufactured in glass reinforced plastics. Larger pressure filters are manufactured in specially coated steel. Operation and performance are generally as described for the rapid gravity filter (see below) and similar facilities are required for backwashing and disposal of the dilute sludge. A similar range of contaminants can be removed depending on the filter medium.
Membranes
Membrane processes used in water treatment are reverse osmosis, ultrafiltration, microfiltration and nanofiltration. Membrane processes can provide adequate removals of pathogenic bacteria, Cryptosporidium, Giardia, and potentially, human viruses and bacteriophages. However, they should not be relied upon as the sole means of disinfection as in the case of the types of systems encountered in private supplies there is no simple means to check membrane integrity to warn of potential breakthrough of microorganisms. Characteristics of membrane processes are illustrated in Figure 1.
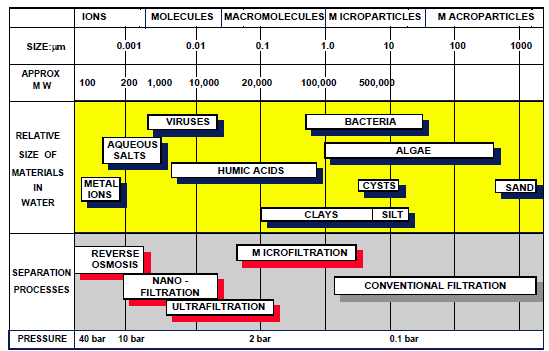
If two solutions are separated by a semipermeable membrane, i.e. a membrane that allows the passage of solvent but not of the solute, the solvent will pass from the lower concentration solution to the higher concentration solution. This process is known as osmosis. It is possible, however, to force the flow of solvent in the opposite direction, from the higher to the lower concentration, by increasing the pressure on the higher concentration solution. The required pressure differential is known as the osmotic pressure and the process as reverse osmosis.
Reverse osmosis results in the production of a treated water stream and a relatively concentrated waste stream. Typical operating pressures are in the range 15 to 50 bar depending on the application. Membrane pore sizes are less than 0.002μm. The most common application of reverse osmosis is desalination of sea water although the use of reverse osmosis for nitrate removal has also been proposed. In the case of private water supplies, reverse osmosis units sold as point of use devices are probably the most common type of membrane process encountered.
Ultrafiltration is similar in principle to reverse osmosis, but the membranes have much larger pore sizes (typically 0.002 to 0.03μm) and operate at lower pressures. Ultrafiltration membranes reject organic molecules of molecular weight above 800 and usually operate at pressures less than 5bar.
Microfiltration is a direct extension of conventional filtration into the sub-micron range. It is capable of sieving out particles greater than 0.05μm and will remove most bacteria and amoeboid cysts. It has been used for water treatment in combination with coagulation or powdered activated carbon (PAC) to remove viruses, bacteria, dissolved organic carbon and to improve permeate flux. Microfiltration membranes have pore sizes typically in the range 0.01 to 12μm and do not separate molecules but reject colloidal and suspended material at operating pressures of 1 to 2bar.
Nanofiltration uses a membrane with properties between those of reverse osmosis and ultrafiltration membranes; pore sizes are typically 0.001 to 0.01μm. Nanofiltration membranes allow monovalent ions such as sodium or potassium to pass but reject a high proportion of divalent ions such as calcium and magnesium and organic molecules of molecular weight greater than 200. Operating pressures are typically about 5bar. Nanofiltration may be effective for the removal of colour and organic compounds.
Screens
Screens are effective for the removal of particulate material and debris from raw water and are used on many surface water intakes. Coarse screens will remove weeds and debris while band screens or microstrainers will remove smaller particles including fish and may be effective in removing large algae. Microstrainers are used as a pre-treatment to reduce solids loading before coagulation or subsequent filtration. A microstrainer may consist of a rotating drum fitted with very fine mesh panels, or may be a fixed mesh that the water flows through. The mesh will ensure that suspended solids, including algae, are retained. The extent of solids removal will be determined by the mesh size and the nature of the raw water. Water will need subsequent treatment downstream and screens should only be considered as a preliminary treatment stage.
Gravel filters
Gravel filters may be used to remove turbidity and algae. A simple gravel filter for the protection of a stream or river inlet is described in Section 3.3.1. A larger gravel filter may consist of a rectangular channel or tank divided into several sections and filled with graded gravel (size range 4 to 30mm). The raw water enters through an inlet distribution chamber and flows horizontally through the tank, encountering first the coarse and then the finer gravel. The filtered water is collected in an outlet chamber. Solids removed from the raw water accumulate on the floor of the filter. Gravel filters can operate for several years before cleaning becomes necessary. The size of a gravel filter will depend on water quality, flow rate and size of gravel. A filter can be up to 12m long, 2 to 5m wide and 1 to 1.5m deep. The filter should normally be sized for a flow rate of between 0.5 to 1.0 cubic metres per square metre of filter surface area per hour (m3/m2.h). A gravel filter will need subsequent treatment downstream, and should only be considered as a preliminary treatment stage.
Slow sand filters
Slow sand filters, sometimes preceded by microstrainers or coarse filtration, are used to remove turbidity, algae and microorganisms. Slow sand filtration is a simple and reliable process and is therefore often suitable for the treatment of small supplies provided that sufficient land is available. Slow sand filters usually consist of tanks containing sharp sand (size range 0.15-0.30mm) to a depth of between 0.5 to 1.5m. For small supplies, modular units of 1.25m diameter are available – a tandem installation would occupy a concrete apron of about 8 to 10 m2. The raw water flows downwards and turbidity and microorganisms are removed by filtration in the top few centimetres of the sand. A biological layer of sludge, known as the schmutzdecke, develops on the surface of the filter that can be effective in removing microorganisms. Treated water is collected in underdrains or pipework at the bottom of the filter. The top few centimetres of sand containing the accumulated solids are removed and replaced periodically. Filter runs of between 2 and 10 weeks are possible, depending on raw water quality and flow rate. Slow sand filters are often operated in tandem; one in service whilst the other is cleaned and time allowed for the schmutzdecke to re-establish. A variant of the slow sand filter, the “Inverness filter”, has been widely used in Scotland. It uses the same grade of sand and operates at the same flow rate as the traditional slow sand filter but the water flows upwards. Filtration is achieved throughout the filter bed and a true schmutzdecke does not develop. The sand is “washed” by opening a valve at the bottom of the filter and allowing the filter bed to drain rapidly. Sand filters should be sized for a water flow rate of between 0.1 and 0.3 m3/m2.h. The flow rate should be controlled and the filter designed with a treated water reservoir of sufficient capacity to accommodate fluctuations in demand, and thus permit operation of filters at a steady and continuous rate.
Rapid gravity filters
Rapid gravity filters are most commonly used to remove floc from coagulated waters. They may also be used to remove turbidity, algae and iron and manganese from raw waters. Granular activated carbon media may be used to remove organic compounds. Rapid gravity sand filters usually consist of rectangular tanks containing silica sand and/or anthracite media (size range 0.5 to 1.0 mm) to a depth of between 0.6 and 1.0m. The water flows downwards and solids become concentrated in the upper layers of the bed. Treated water is collected via nozzles in the floor of the filter. The accumulated solids are removed periodically by backwashing with treated water, usually preceded by scouring of the media with air. Frequency of backwashing depends on loading rate and raw water quality and is typically every 24 hours. Backwashing can be initiated automatically after a predetermined headloss has been reached or may be carried out manually. Backwash flowrates will be stipulated by the manufacturer. It is important to achieve the required bed expansion in order to ensure filters are washing properly, but care must be taken to prevent loss of media with too high a flowrate. A dilute sludge that requires disposal is produced which may be discharged to sewer, soak away, or after treatment, to a watercourse provided that any required discharge consent is obtained.
Coagulation and flocculation
Coagulation and flocculation are used to remove colour, turbidity, algae and other microorganisms from surface waters. The addition of a chemical coagulant to the water causes the formation of a precipitate, or floc, which entraps these impurities. Iron and aluminium can also be removed under suitable conditions. The floc is separated from the treated water by sedimentation and/or filtration, although flotation processes may be used in place of sedimentation.
The most commonly used coagulants are aluminium sulphate and ferric sulphate, although other coagulants are available. Coagulants are dosed in solution at a rate determined by raw water quality near the inlet of a mixing tank or flocculator. The coagulant is rapidly and thoroughly dispersed on dosing by adding it at a point of high turbulence. The water is allowed to flocculate and then passes into the sedimentation tank (sometimes known as a clarifier) to allow aggregation of the flocs, which settle out to form sludge. This sludge will need to be periodically removed.
The advantages of coagulation are that it reduces the time required to settle out suspended solids and is very effective in removing fine particles that are otherwise very difficult to remove. Coagulation can also be effective in removing many microorganisms. The principal disadvantages of using coagulants for treatment of small supplies are the cost and the need for accurate dosing, thorough mixing and frequent monitoring. Coagulants need accurate dosing equipment to function efficiently and the dose required depends on raw water quality that can vary rapidly. The efficiency of the coagulation process depends on the raw water properties, the coagulant used and operational factors including mixing conditions, temperature, coagulant dose rate and pH value. The choice of coagulant and determination of optimum operating conditions for a specific raw water are normally determined by bench scale coagulation tests. Thus, while coagulation and flocculation are the most effective treatment for removal of colour and turbidity they may not be suitable for private supplies because of the level of control required and the need to dispose of significant volumes of sludge.
Sedimentation
Simple sedimentation (i.e. unassisted by coagulation) may be used to reduce turbidity and solids in suspension. Sedimentation tanks are designed to reduce the velocity of flow of water so as to permit suspended solids to settle under gravity. There are many different designs of tanks and selection is based on simple settlement tests or by experience of existing tanks treating similar waters. Without the aid of coagulation, these will only remove large or heavy particles, and due to the length of time this process will take, the system will usually require storage tanks to balance peaks and troughs in demand.
Sedimentation tanks are usually rectangular with length to width ratios between 2:1 and 5:1. The depth of the tank is usually between 1.5 and 2.0m. The inlet and outlet must be at opposite ends of the tank. The inlet should be designed to distribute the incoming flow as evenly as possible across the tank width and to avoid streaming which would otherwise reduce sedimentation efficiency. Baffles may be installed to prevent short circuiting. The outlet should be designed to collect the clarified water over the entire tank width. The tank should be covered to prevent contamination and ingress. Sedimentation tanks require cleaning when performance deteriorates. This will not normally be more frequent than once per year.
Aeration
Air stripping is used for removal of volatile organics (e.g. solvents), carbon dioxide, disinfection by-products, some taste and odour causing compounds, and radon. It is a fairly specialist technique, and not commonly found as a treatment process on private water supplies, although aeration can sometimes be found in the oxidation stage of the treatment process for the removal of iron and manganese. Aeration processes are designed to achieve efficient mass transfer of oxygen into water and removal of gases and volatile compounds by air stripping. Oxygen transfer can usually be achieved using a simple cascade or diffusion of air into water, without the need for elaborate equipment. Stripping of gases or volatile compounds, however, may require specialised plant that provides a high degree of mass transfer.
For oxygen transfer, cascade or step aerators are designed so that water flows in a thin film to achieve efficient mass transfer. Cascade aeration may introduce a significant headloss; design requirements are between 1.0 and 3.0m to provide a loading of 10 to 30m3/m2.h. If such headloss is unacceptable the alternative is to use compressed air diffused through a system of submerged perforated pipes. These types of aerator are used for oxidation and precipitation of iron and manganese. To achieve air stripping various techniques can be used including counter current cascade aeration in packed towers, diffused aeration in basins and spray aeration. Packed tower aerators are most commonly used because of their high energy efficiency and compact design.